Julie Bellemare, N. Astrid R. van Giffen, and Robert Schaut
Since 2019, the Corning Museum of Glass has been investigating the making of its “realgar-colored” glass objects. A Chinese innovation, this red and orange glass was developed in the early decades of the eighteenth century and used at the Qing imperial glassworks to create a range of vessels, but the secret to its making was subsequently lost. What is today commonly referred to as “realgar glass” is a yellow-to-red-colored glass developed in China during the eighteenth and nineteenth centuries. The term “realgar-colored glass” (xionghuangse boli 雄黃色玻璃) connects the mottled and variegated surface effects of the glass with those of the realgar mineral, but this term was not used to describe this glass at the Qing imperial workshops. Instead, the term “persimmon glass” (shihuang boli 柿黃玻璃) was used, which better describes the more monochrome opaque orange color of early imperial versions of this glass (Fig. 1).[1] Objects made later, and some without imperial marks, tend to feature a characteristic yellow-to-red mottling as well as an external layer of translucent red glass (Fig. 2).
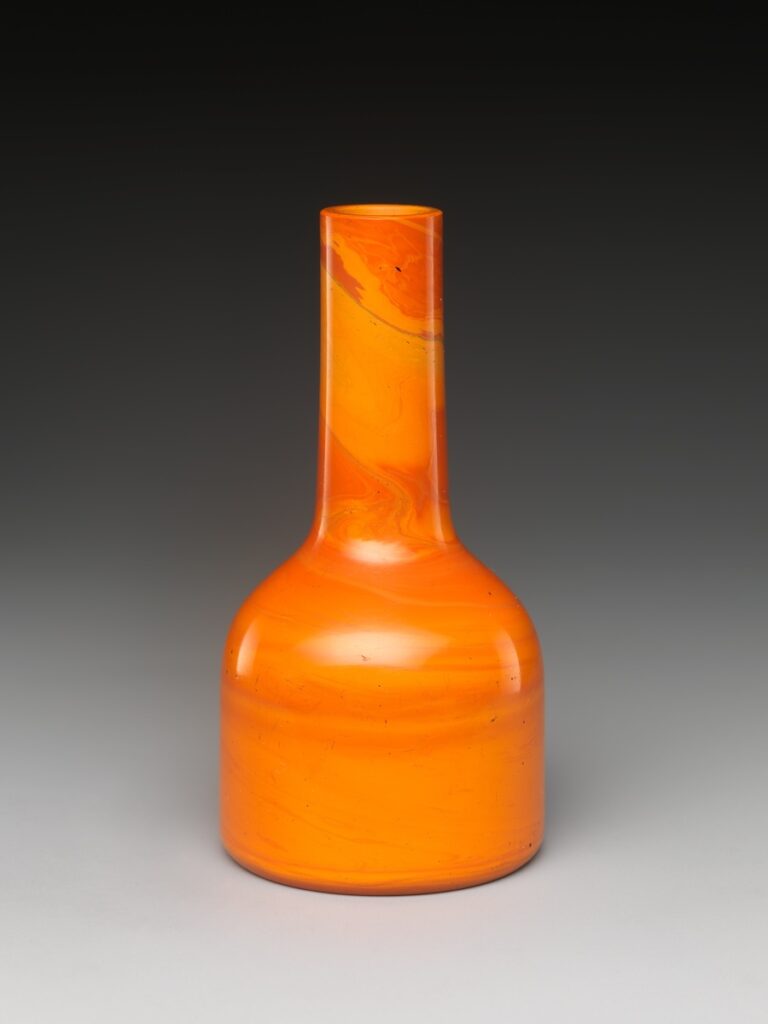
To better understand the composition and making of this glass, we conducted elemental analysis and partnered with materials scientists at Corning Incorporated, a company specializing in advanced glass and ceramic technologies, to mix the ingredients and recreate this historical glass recipe in the lab. We then brought this raw glass back to the Museum, where it was blown and formed by the Museum’s glassblowers in wood-burning and gas furnaces. Experimenting with different fuel types and mold materials, we have gained further insights into how eighteenth-century glassblowers might have worked with this unique material. This short paper will report on this process and the knowledge gained from the recreation of realgar-colored glass in the lab and in the hot shop, advocating for the importance of experimental research methods to art historical inquiry. This reconstruction project allows us to consider both the laboratory and the hot shop as places of knowledge production, each providing different insights into this special glass and the objects made from it.
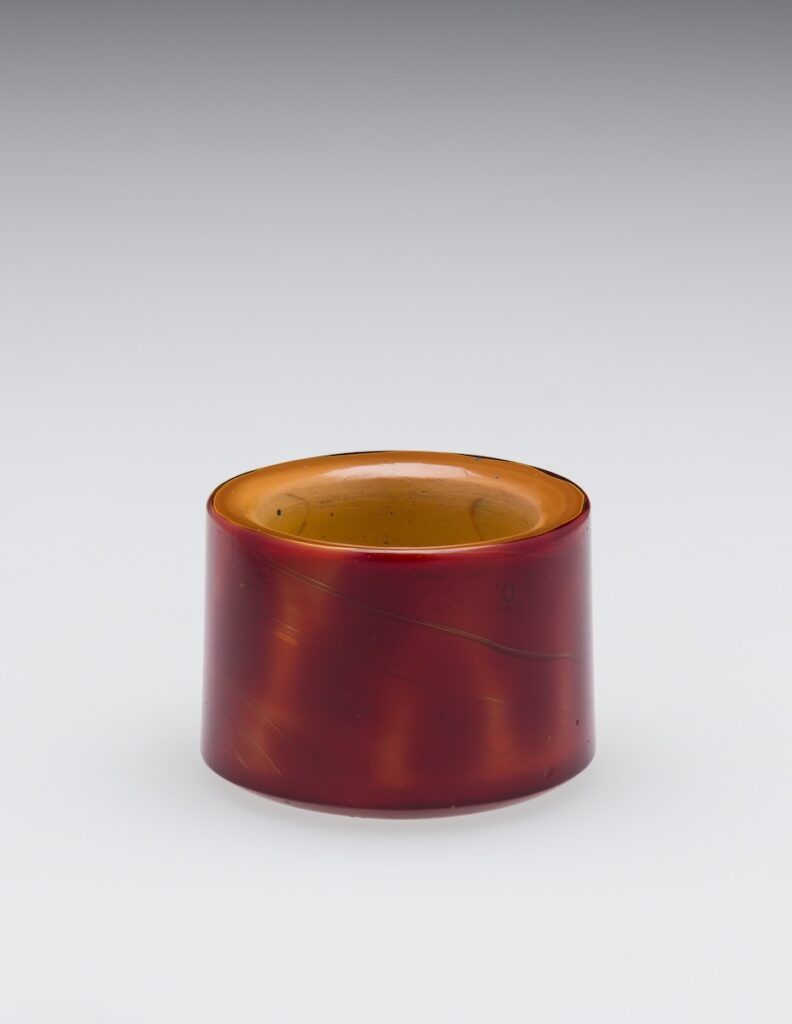
Moving from the archive to the research lab, and using two types of glass furnaces, our approach is a form of technical art history, which combines expertise from conservators and scientists to understand an object’s materials and making process, usually leading to an enhanced art historical interpretation of that object.[2] Under the broad umbrella of technical art history is experimental archeology, a means of testing hypotheses by recreating objects to understand their function, or how they were made.[3] This approach is often tied to archeological investigations, and, by extension, to a body of objects generally made much earlier than the early modern period. Recent experimental research into early modern craft includes academic initiatives, for instance, the Making and Knowing project at Columbia University, and ARTECHNE—Technique in the Arts, 1500–1950 at Utrecht University, both of which have recreated recipes found in texts and manuals.[4] Some of these hands-on experimental approaches have informed museum exhibitions, such as Remaking the Renaissance at the University of Wisconsin-Madison’s Center for Design and Material Culture, which considers early modern textile innovations through conservation, scientific testing, and reconstruction.[5]
Recent scientific analyses of realgar- or persimmon-colored glass in several museum collections, including our own, have shown its variegated surface effects were not the result of mixing different colorants or glass batches, but were all created by a single composition.[6] These findings raised the possibility that the red, orange, and yellow colors were created instead by variations in temperature, but this hypothesis could not be tested by traditional research methods such as historical research and chemical analysis.
The Limits of Archival Research and Scientific Testing
When it comes to research into Chinese glass, archival and historical inquiry faces several limitations. The main source of information on craft production in the Qing dynasty (1644–1911) is the Archives of the Imperial Workshops, which include highly detailed records compiled from 1723 until the end of the dynasty.[7] Although these archives contain a wealth of information on commissions of glass objects, there is virtually no mention of recipes or detailed making processes. What was produced was more important than how it was produced. For instance, a typical entry might mention that on the 21st day of the second month of the seventh year of the Qianlong reign (equivalent to March 27, 1742), a palace eunuch handed over to the glass workshop a persimmon glass vase for holding incense implements, and that just over a month later, a matching glass incense box was collected.[8] What took place at the glass workshop during that month remains absent from the written record. The workshop officials wrote for the emperor and his administration, not for the artisans and craftspeople, who would have instead learned their craft through apprenticeship, by making and doing.
Faced with this lack of textual information, our team turned to objects. Beyond visual examination, it was clear that scientific testing would be required to understand the composition of the persimmon- and realgar-colored glass objects in the Corning Museum of Glass collection. Our first step was to carefully examine each object to see what it could tell us about how it was made. From this, we learned that objects were often mold-blown, as evidenced by the presence of seam lines, and all were polished once cooled. Some objects have color variations that indicate the use of elaborately decorated molds. We also noted that generally transparent red areas were thinner than opaque yellow areas and that the red was often a distinct thin layer on top of a core of orange persimmon.
Next, we analyzed our objects using a portable X-ray fluorescence spectrometer (pXRF), a non-destructive method to determine a semi-quantitative composition of a glass. XRF is a great place to start when identifying a glass composition, but it has limitations because it cannot detect lighter elements like sodium and boron, which are often main ingredients in glass. Our initial results showed that the various colors all had essentially the same composition (with copper as the main colorant) but could not explain the existence of different colors. The presence of a broken realgar-colored snuff bottle in our collection enabled more extensive scientific analyses to better understand the color variations of this glass. These analyses, which could not accommodate our intact objects due to size limitations and which required the sacrifice of one tiny fragment for some applications, included micro-scale XRF, X-ray diffraction (XRD), electron microprobe analysis (EPMA), and scanning transmission electron microscopy (STEM) and were done with our partners at Corning Incorporated. Our team tested the yellow, orange/brown, and red portions of the glass. In addition to a complete quantitative composition for the glass, the analyses showed that the coloring agent in all colors was copper (I) oxide, in the form of cuprite crystals, and that the main difference between the colors was the size of the cuprite crystals in the glass. We hypothesized that differences in the temperature and cooling rates during the making process were responsible for the variation in crystal sizes and therefore the colors, but we could not pinpoint what those differences were. We had reached the limit of what we could explain with chemical analyses. To put our hypothesis to the test, we would need to recreate the glass.
Reverse-Engineering Glass in the Lab
This project played to the unique strengths of the Corning Museum of Glass, namely its encyclopedic collection, expertise in various aspects of glass history and making, and a longstanding partnership with Corning Incorporated scientists. The µXRF and EPMA analyses of the broken snuff bottle provided quantitative concentrations of the elements present but provided no details as to their original raw materials, their origin, or the making process.[9]
These realgar-glass compositions are very interesting to the scientific community working in industry for two reasons. First, modern glass science history, which has traditionally focused on Western glassmaking, purports that three German chemists, Otto Schott (1851–1935), Ernst Abbe (1840–1905), and Carl Zeiss (1816–1888), were the first to introduce boron oxide to glass in the late 1800s. Supposedly all glasses prior to this period were traditional soda-lime-silicate glasses, and their introduction of boron led to the creation of low-expansion glasses for microscope and telescope lenses. But these eighteenth-century realgar glass artifacts contain ~20% by weight (denoted wt%) boron oxide (much more than the 8–12wt% in modern borosilicate glasses), indicating that boron was intentionally sourced and added to the formulation. Boron is a relatively rare element on earth and is mined in only a few locations worldwide, largely in Turkey and southwestern United States. The fact that the Qing dynasty could source this rare element for glass melting in high volumes is remarkable and speaks to mature trade routes and advanced knowledge about the origins and value of boron-containing minerals.[10]
Second, realgar glasses contain a high concentration of arsenic oxide (4–5wt%). While this oxide does not contribute to coloration itself, it likely provides reducing power—meaning that it keeps copper dissolved in the melt and favors the red colloidal coloration instead of the more oxidized copper II (typically colored blue). Without arsenic, these realgar glasses would yield a blue-brown coloration. As with boron, the high arsenic concentrations used in these glasses speak to an ability to source individual raw materials and understand their importance to the glass batch. Modern glassmaking uses traces of arsenic (0.01–0.05wt%) to assist in bubble removal from glass melts, but rarely uses it otherwise.
NC-ND.
Fortunately, modern technical glass batching labs have access to a wide variety of raw materials featuring nearly every element on the periodic table. After considering those raw materials typically used (sand, borax, copper oxide, arsenic oxide, limestone, soda ash) and their appropriate ratios, we calculated a batch that would yield the corresponding glass chemistry after the high temperature melting reactions. Individual raw materials were weighed, combined, and mixed thoroughly before being placed in a crucible for melting (Fig. 3).
CC-BY-NC-ND.
The crucible containing the well-mixed raw ingredients was heated in an electric furnace to promote melting and homogenization of the liquid. We initially selected 1200°C for melting of the boron- and copper-rich batch but found that the raw sand grains were not completely incorporated after 6 hours. Increasing the temperature to 1300°C created a well-mixed and fully melted liquid with low viscosity. Pouring this melt into a mold or onto a steel table produced a high-quality glass slab which was subsequently annealed (Fig. 4). Once annealed and cooled to room temperature, the variation in glass color became visible, displaying the full range of colors present in the museum’s artifacts and the most variation where the melt cooled in different ways (fast and slow-cooled glasses looked different).
Building on the prior observation that copper oxide crystals were responsible for coloration, we hypothesized that they would nucleate (form first crystal structure on nanometer scale) and grow at different temperatures like modern glass ceramic materials. To explore this material behavior, we first made samples of glass that had been rapidly cooled to minimize growth of the copper crystals and we noted that these materials were dark, translucent, and ruby red. When these glasses were reheated to softening temperatures, the crystals grew larger, the material became opaque, and the color shifted toward orange persimmon. We identified that the glass required heat treatment between 600°C and 700°C for five to fifteen minutes to allow these crystals to grow. At these temperatures, the glass is viscous enough to retain its shape while allowing its atoms to move and arrange into increasingly larger crystals. The larger crystals scatter more light, increasing the opacity as the color shifts from red to yellow and orange. This enabled the glassmaker to control whether the glass was in either one of these states (translucent red or opaque persimmon).
Forming Objects in the Hot Shop
Achieving the right coloration in the glass that was batched, melted, and poured at Corning Incorporated confirmed that the glass chemistry was correct. Laboratory experiments showed that heating and cooling were key to controlling the coloration and pinpointed the temperature range needed to create the color variations, but we also wanted to understand how eighteenth-century glassmakers would have worked with this material to create the objects that survive today.
With several pounds of glass cullet generously donated to the museum by the company, we enlisted the help of the museum’s Hot Glass team, who typically perform glassmaking demonstrations for the public. Glassblowers in the Hot Glass team were unaccustomed to working with this type of glass, and their insights were invaluable to understanding how its working properties compare to modern glasses. In the spring and summer of 2023, they built a fully functional wood-burning furnace in the museum’s courtyard hot shop. The furnace was initially constructed to support our special exhibition, Dig Deeper: Discovering an Ancient Glass Workshop, which explored fourth-century glass production in Jalame, modern Israel.
of the Corning Museum of Glass. CC-BY-NC-ND.
On a warm July morning, the team stoked the fire and melted the glass in a crucible at the heart of the furnace (Fig. 5). We wanted to know if the glass could be melted and formed at the lower, and more variable, temperatures afforded by this type of fuel (as opposed to the modern gas furnaces used in hot shops today), since imperial workshop records mention the use of firewood and coal in glass furnaces in the Qianlong period.[11] We also wanted to test a few mold materials (namely wood, ceramic, aluminum, and steel) to see whether their different rates of heat absorption would have a noticeable effect on the coloration and patterning of the glass. This exploratory phase revealed that this glass behaves quite differently from the soda lime glass we use for demonstrations. Jesse Rasid, Hot Glass Programs Senior Technician, described the glass as “much softer and runnier than modern glasses and hard to control.” Jeff Mack, Manager of Hot Glass Programs, added that, “it had a long viscosity curve which allowed extended working time with the glass before it required reheating.” They both noted the effect of temperature fluctuations and the firing atmosphere on the color.[12] The team further found that polishing and carving (known as cold working in the glass world) was key to revealing the colors and patterns of the glass. In cold working, the glass feels similar to modern glass but has a tendency to chip and flake apart at the edges when being cut. Experimenting with a different kind of glass led to many insights into its working properties when hot and cold, but the precise effects of mold materials remain unclear.
A second round of experiments, this time in a modern gas furnace, considered the importance of thermal variation in the creation of an opaque persimmon core, and a translucent red overlayer. Previous observations demonstrated that this “layering” did not appear to be a result of separate gathers (a gather is a mass of molten glass collected on the end of a blowpipe or pontil) but was rather due to intentional heating and cooling during forming.
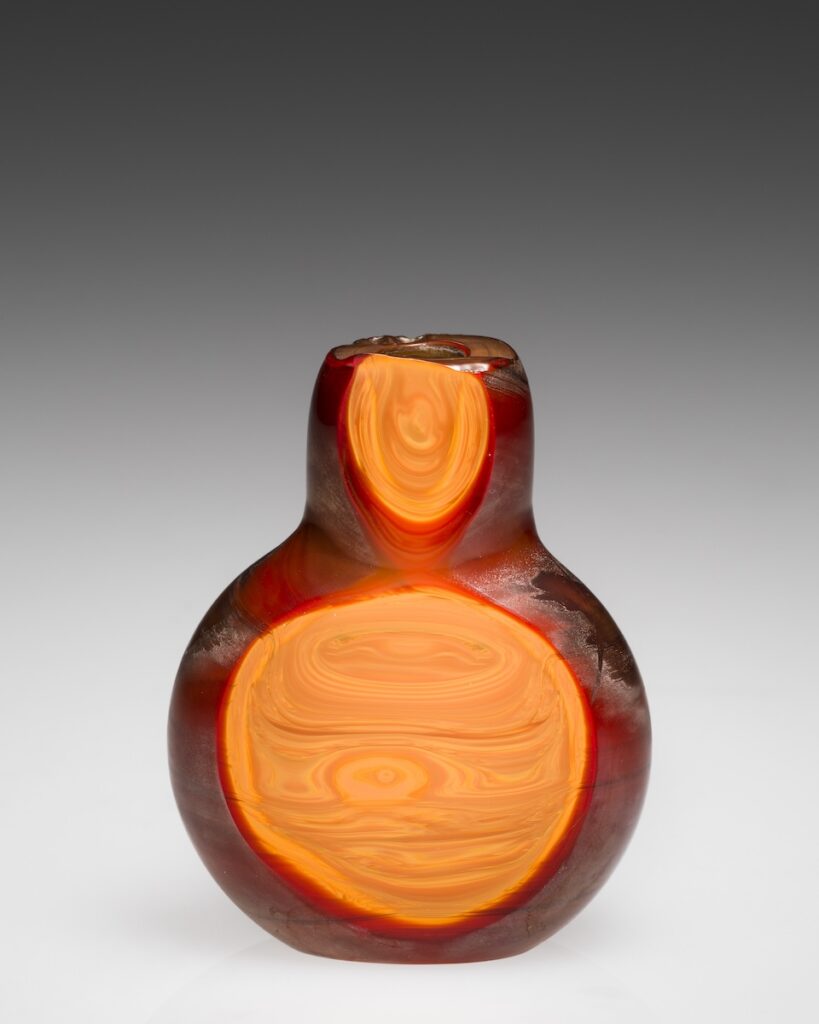
Those who have ever attempted to temper chocolate will know that this fickle ingredient needs to be slowly heated up to a precise temperature, cooled to a lower temperature, and sometimes (depending on the method) reheated to a middling temperature before it can finally gain a satisfying sheen and snappy texture. Our experiments revealed that realgar-colored glass needs to be “tempered” in a similar way. The molten gather would be formed to the desired shape first, using a variety of tools and molds. Still attached to the pipe, the glass object would be held in a furnace at a constant temperature to allow time for crystals to grow. This was hotter than annealing, but below the temperature at which the glass flows rapidly. If the process stopped here, the result would be an opaque persimmon object. In certain cases, however, the object’s surface would then be rapidly heated to melt back the opacity-causing crystals and quenched to lock in the translucent red coloration. This specific thermal history is needed to impart the cameo-like layering of translucent red atop an opaque persimmon base. This round of experiments successfully resulted in objects with a persimmon core and red outer later, made more visible when the object is ground and polished (Fig. 6).
In addition to understanding more about the coloration process, blowing and forming this glass in the hot shop also revealed how small vessels like snuff bottles were produced. By making several bottles in a row, our glassblowers soon realized that they could skip the step of transferring the object from the blowpipe to the pontil (also called punty), a step that is usually essential to forming a vessel’s opening. Instead, because the narrow mouths of snuff bottles did not need to be opened, they could easily be knocked off the blowpipe and finished by cold working. This removed one step at the furnace while adding one at the cold working shop, but since most bottles were already extensively carved and polished, refining the mouth would not have strained the worker’s capacity. As a result, these small bottles could be produced at a much faster rate.
Conclusion
The recreation process confirmed that realgar glass could be melted, formed, shaped, and heat treated with the technologies known to be available in China in the first half of the eighteenth century. The complexity of the heat treatment required to create these colored layers from a single glass composition demonstrates that the original makers had deep knowledge of the material’s behavior. The creation of vessels with solid persimmon and cameo-like colorations would have required multiple furnaces operating at different temperatures or the ability to rapidly adjust the temperature during the process of making a vessel.
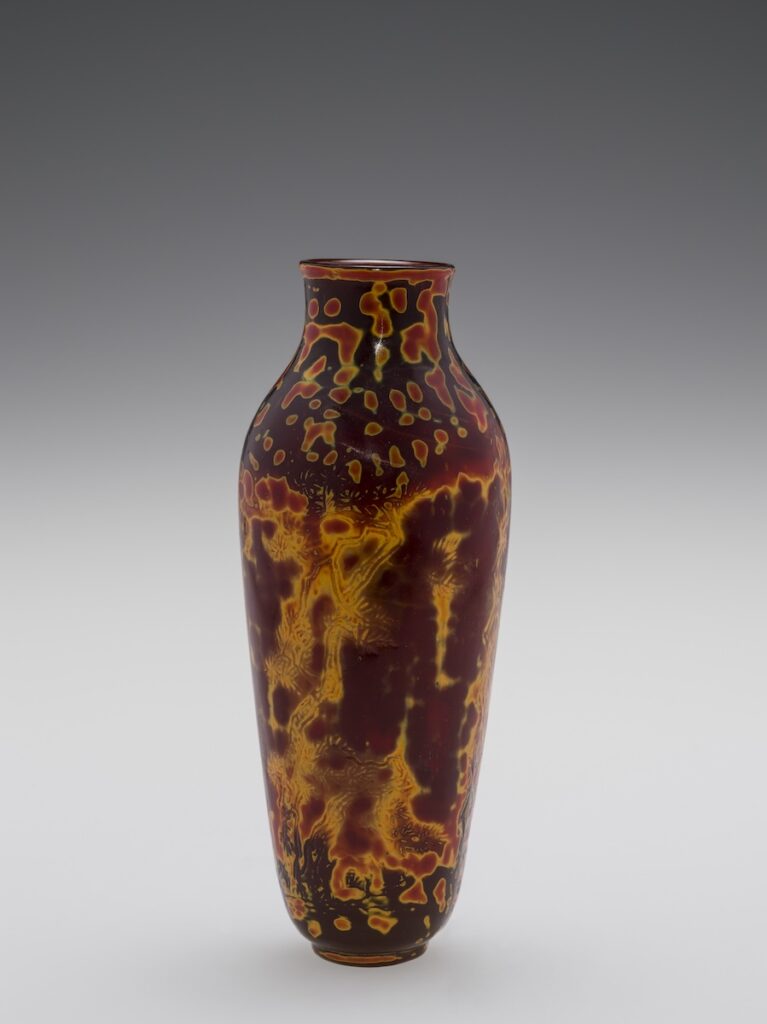
These experiments are ongoing. We initially focused on heat variations, mold materials and the recreation of one type of color combination, namely persimmon cores and red outer layers. But what are the precise effects of molds in the creation of pictorial patterns on the glass? In the next few months, we plan to sharpen our understanding of surface effects by commissioning a custom mold to clarify how a convex or concave surface design in the mold impacts the coloration of a pattern after the piece is polished. This will help illuminate how another group of realgar-glass objects were created, for instance, a small vase with a pictorial design of pine trees (Fig. 7). Moving forward with this project, we will shift our focus to other variations of this type of glass, which do not have a strong persimmon core and feature more translucent red.
As we plan to disseminate these findings in the museum’s physical displays and online platforms, questions remain as to how to best convey the making process to an audience largely unfamiliar with the making of glass, let alone realgar glass. Beyond gallery design, how can the reconstruction process be made more visible to museum visitors? We have been documenting this process by keeping samples from various stages and thinking about using these test pieces to show the process step-by-step in a gallery setting. Reconnecting with ancient craft practices through object displays and digital media is a promising way to get museum visitors engaged with the objects on view. More generally, this kind of initiative provides further opportunities to leverage expertise in other museum departments, such as education and public programs, to create well-rounded, engaging, and accessible learning experiences for museum visitors.
This project has shown that reconstruction can be key to understanding objects, notably their material composition and how they were created. Recognizing the unique characteristics and behavior of realgar glass relied on a range of expertise, including that of conservators, art historians, scientists, and makers. By moving through this process, our team members broke down barriers between disciplines and arrived at a fuller understanding of a specific material, thus expanding the study of glass to consider the unique technical innovations of Qing-dynasty glassmakers.
Julie Bellemare is Curator of Early Modern Glass at the Corning Museum of Glass
N. Astrid R. van Giffen is Conservator of Ancient through Modern Glass at the Corning Museum of Glass
Robert Schaut is Research Fellow at Corning Incorporated
[1] Julie Bellemare, Federico Carò, and Karen Stamm, “Persimmon and Peonies: Orange-Colored Glass and Enamels from the Qing Imperial Workshops,” Metropolitan Museum Journal 58 (2023), 96–106.
[2] Erma Hermens, “Technical Art History: The Synergy of Art, Conservation and Science,” in Art History and Visual Studies in Europe: Transnational Discourses and National Frameworks (Leiden: Brill, 2012), 151–65, https://doi.org/10.1163/9789004231702_012.
[3] Christina Souyoudzoglou-Haywood and Aidan O’Sullivan, eds., Experimental Archaeology: Making, Understanding, Story-Telling (Oxford: Archaeopress, 2019), https://doi.org/10.2307/j.ctvpmw4g8.
[4] Making and Knowing Project – Intersections of Craft Making and Scientific Knowing; ARTECHNE – Technique in the Arts, 1500-1950 | Technique in the Arts, 1500-1950: Concepts, Practices, Expertise | About the project (uu.nl); see also Sven Dupré, Anna Harris, Julia Kursell, Patricia Lulof, and Maartje Stols-Witlox, eds., Reconstruction, Replication and Re-enactment in the Humanities and Social Sciences (Amsterdam: Amsterdam University Press, 2020).
[5] Remaking the Renaissance – Center for Design and Material Culture – UW–Madison (wisc.edu).
[6] Shelly Xue and Christopher L. Maxwell, Asian Glass: Selections from the Corning Museum of Glass (Corning, NY: The Corning Museum of Glass, 2022); Bellemare, Carò, and Stamm, “Persimmon and Peonies”; Hongjiao Ma, Julian Henderson, Jianfeng Cui, Kunlong Chen, “Glassmaking in the Qing Dynasty: A Review, New Data, and New Insights,” Advances in Archaeomaterials 1 (2020), 27–35.
[7] Zhongguo di yi lishi dang’an guan, Xianggang zhongwen daxue wenwu guan (China First Historical Archives, Chinese University of Hong Kong Art Museum), Qinggong neiwufu zaobanchu dang’an zonghui [Collected archives of the workshops of the Qing Imperial Household Department], 55 vols. (Beijing: Renmin chubanshe, 2005). The entries for 1796 to 1911 are neither published nor digitized, and can only be accessed in person at China First Historical Archives in Beijing, or as facsimiles at the National Palace Museum Library, Taipei.
[8] Zhongguo di yi lishi dang’an guan, Qinggong neiwufu zaobanchu dang’an zonghui (Beijing: Renmin chubanshe, 2005), 11:62-63.
[9] See the chemical composition tables in Xue and Maxwell, Asian Glass: Selections from the Corning Museum of Glass (Corning, NY: The Corning Museum of Glass, 2022), 144–155.
[10] Although little is known about Qing sources of boron, the imperial administration orchestrated multiple mining and prospecting operations in the outer reaches of the empire. See Nanny Kim, “Copper Transports out of Yunnan, ca. 1750–1850: Transport Technologies, Natural Difficulties and Environmental Change in a Southwest Highland Area,” in Metals, Monies, and Markets in Early Modern Societies: East Asian and Global Perspectives 1, ed. Thomas Hirzel and Nanny Kim (Berlin: Lit, 2008), 191–220; Yulian Wu, “Chimes of Empire: The Construction of Jade Instruments and Territory in Eighteenth-Century China,” Late Imperial China 40, no. 1 (2019): 43–85, https://doi.org/10.1353/late.2019.0002.
[11] Modern gas furnaces are usually operated at 2100°F (1150°C), while our wood-burning furnace was typically around 1900°F (1038°C), with the highest temperature recorded at 2150°F (1177°C), depending on the type and quality of wood used. The wood-burning furnace required stoking the fire every fifteen to twenty minutes, resulting in variations in temperature. Zhongguo di yi lishi dang’an guan, Qinggong neiwufu zaobanchu dang’an zonghui (Beijing: Renmin chubanshe, 2005) 12, no. 11; 18:850-853.
[12] Jeff Mack and Jesse Rasid, personal communications, January 31 and February 1, 2024.
Cite this article as: Julie Bellemare, N. Astrid R. van Giffen, and Robert Schaut, “Hot Tempered: Recreating a Lost Glass Recipe,” Journal18, Issue 18 Craft (Fall 2024), https://www.journal18.org/7481.
Licence: CC BY-NC
Journal18 is published under a Creative Commons CC BY-NC International 4.0 license. Use of any content published in Journal18 must be for non-commercial purposes and appropriate credit must be given to the author of the content. Details for appropriate citation appear above.