Philippe Colomban
While much scholarly attention has been paid to the early modern European quest to discover and master the technologies of Chinese porcelain, Chinese attempts to mimic European surface effects remain relatively unexamined. Within this complex technological competition, China became the “workshop of the world” for producing enameled objects using European ingredients and designs, not only for the Qing Court and Chinese elites but also for export back to the European market.[1] Scholars have previously used European archives to document the importation of Chinese and Japanese porcelain into Europe, as well as the European search for information on Asian expertise in ceramic production.[2] Attention has now shifted to what the correspondence of Jesuit missionaries can also reveal about the specific knowledge and ingredients China received from Europe.[3] Jesuit sources and archives of the Manchu Court Palace document how European enamel technology entered China, resulting in the passage from a limited chromatic palette—wucai (five colors: blue, green, red, black, and yellow) that cannot be mixed—to more than 30 colors after the incorporation of new mixable versions of the basic palette and the addition of white, pink, and purple.[4] The capacity to mix on a grand scale combined with the pointillist painting technique practiced by French miniaturists thereby offered an almost infinite number of new shades. However, much of the information on the production process of such objects remains inscribed in their materials.
A Brief Introduction to Glazes and Enamel Painting in the Seventeenth Century
European enamelers on metal, in particular those based in Limoges or working for the Court of France who settled in Blois or Paris in the seventeenth century, developed enameling techniques that offered a range of colors equal to that of pastel or oil painting (Fig. 1).[5] Smalt (a cobalt-rich glass), Naples yellow (a lead-tin-antimony pigment), and Bernard Perrot’s ruby or purple of Cassius (both of which employ gold nanoparticles) were typical European colors and ingredients used to achieve sophisticated opaque painted enamels.[6] These coloring agents are sufficiently minute to thoroughly mix and thereby produce an almost infinite variety of colors, and to be applied quiet finely. In the same period, Chinese craftsmen had a very limited palette because their glazes relied solely on transition metals such as iron, copper, and manganese as the coloring agents (Fig. 2).[7] These ions produce colors described as “transparent,” similar in appearance to watercolor, which cannot be mixed to obtain intermediate shades or complexly layered. Due to the glaze technology, seventeenth-century Chinese porcelain decoration was thus either monochrome, bichrome, or trichrome, and it entailed laying a transparent overglaze atop a drawing, such as the famous underglaze blue designs of blue-and-white porcelain.
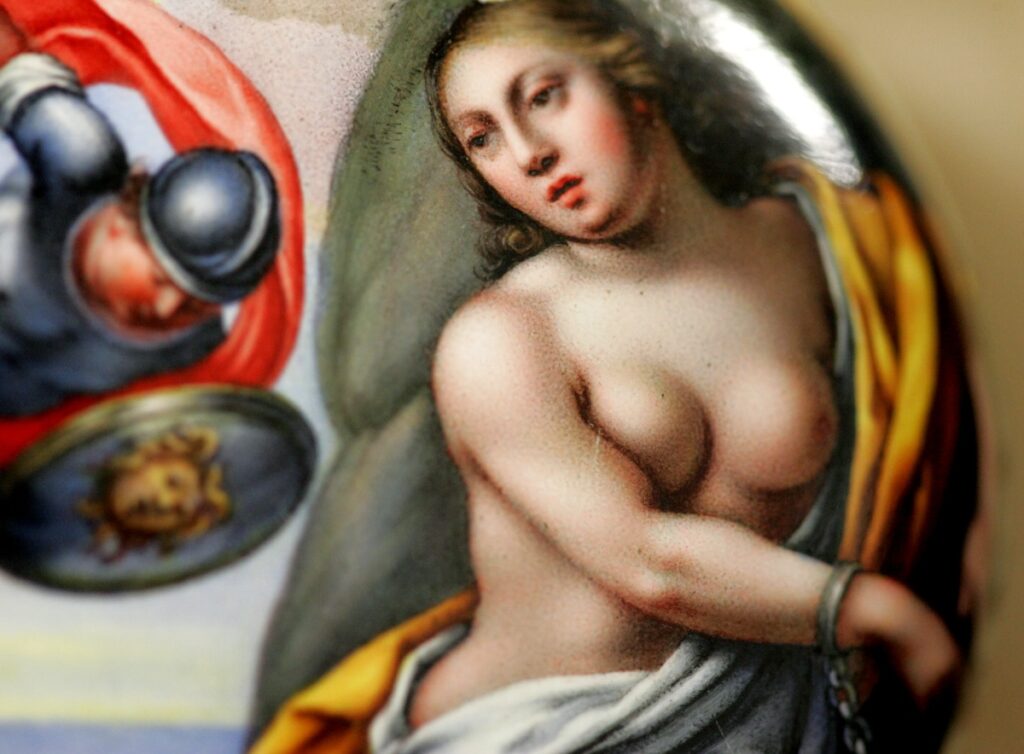
The adoption of European techniques in Chinese workshops, starting at the end of the seventeenth century, greatly widened the palette of Chinese enamels, but also gave rise to new technical constraints.[8] The success of these new chromatic possibilities and their incorporation alongside traditional Chinese glazing techniques is reflected in the rise of Famille verte and Famille rose porcelain, as classified by Albert Jacquemart in 1862.[9] Both classes combine striking new opaque overglaze colors developed from European knowledge and ingredients with a traditional blue-and-white underglaze. The interplay of transparent blue-and-white with European overglazes reflects not only an aesthetic choice, but also the constraints of Chinese kiln technology. Chinese craftsmen used a firing process that employs high temperatures and a reducing atmosphere. These conditions, which were essential to produce white paste porcelain, resulted in copper red (jun, oxblood) and blue-and-white motifs.[10] In the case of the blue underglaze, the raw material used in China to produce blue contains iron, manganese, and cobalt in comparable quantities.[11] This metallic mixture requires a reductive firing process to obtain a true blue color, and otherwise turns dark green or matte black. In contrast, European cobalt is free of iron and manganese and its blue, further magnified by the presence of arsenic, can be fired in an oxidizing atmosphere and at a lower temperature.[12] Chinese craftsmen first employed European colors that could be fired alongside the blue-and-white decorations in the reducing atmosphere of Chinese kilns. These included beautiful opaque yellows and greens and a spectrum from pink to purple. In contrast, several pigments and opacifiers widely used in Europe that do not tolerate high firing temperature, including Naples yellows, remained unknown in China until almost the end of Kangxi’s reign (1661-1722).[13]
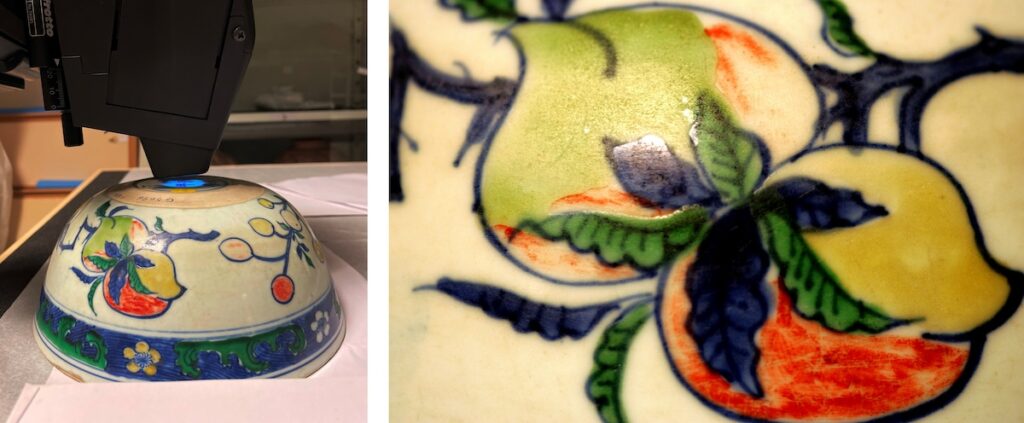
Highlighting European Pigments and Coloring Agents
Technical analysis confirms not only the use of European recipes but also the importation of European raw materials for ceramic production in the Qing Dynasty (1644-1912). These results help identify exactly when this exchange began. One of the clearest markers is cobalt and the associated elements characteristic of the different geological contexts of European mines and Chinese ores.[14] For instance, the source of cobalt used for the mark of bowl G5696 (see Fig. 2) is rich in manganese, indicating a “Ming Chinese” cobalt underglaze applied at the Jingdezhen kilns, while the blue flower is made of lead enamel colored by cobalt combined with nickel and arsenic, i.e., from European smalt provided by Dutch merchants, which had to be fired at a second location.[15]
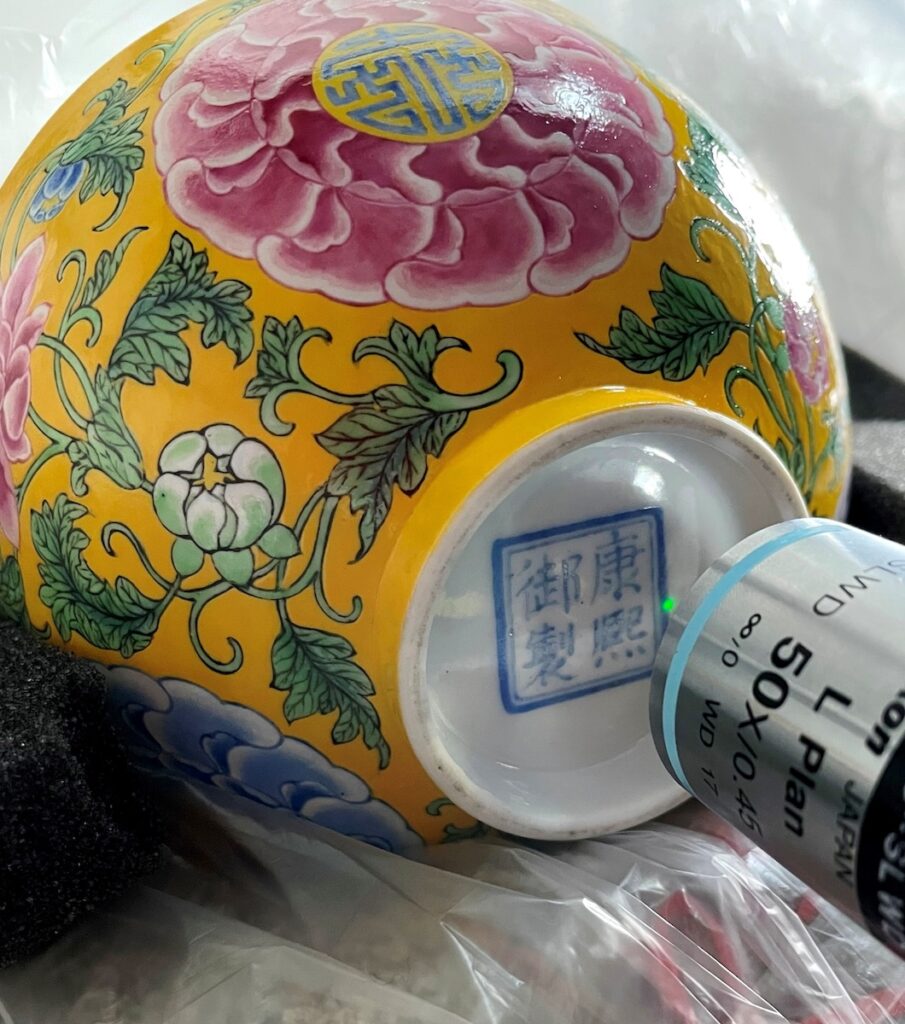
As the above description suggests, the use of imported and domestic cobalt varied between and within objects. For Imperial works of exceptional quality from the end of the reign of Emperor Kangxi, only imported cobalt was used. In other ceramics, such as the Kangxi bowl (Fig. 3), imported cobalt was used for the painted decoration while domestic cobalt (or a mixture) was used for the reign mark. For ceramics from the reign of Emperor Qianlong (1735-96), different cobalts were mixed. These differentiated uses were driven by both economic imperatives (imported cobalt was expensive) and technical constraints. The varied uses of imported cobalt reflect the different firing technologies used in China and Europe. When Chinese craftspeople switched to kilns that employed an oxidizing environment to achieve more complex decorations, they also needed to switch to imported European cobalt that could achieve a saturated blue in that atmosphere.
If the analysis of cobalt demonstrates how the Chinese adoption of European materials was shaped by technical constraints, the study of opacifiers reveals how European techniques also altered the use of local materials. In ceramics from the Qing period, two European methods of opacification begin to appear. While an opacification process that employs a tin oxide was observed in a few (mainly imperial) pieces, an alternative opacification technique that uses lead arsenate was the most common.[16] While the technique was European, technical analysis reveals that Chinese sources of arsenic quickly replaced imported ingredients. In this case, Chinese craftspeople quickly adopted local raw materials to follow European recipes.
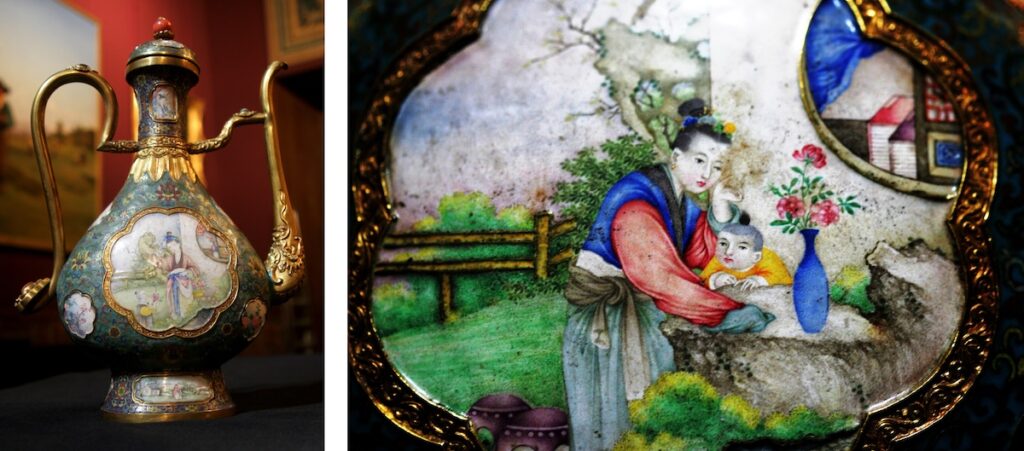
These practices were not consistent throughout the duration of the Qing Empire. From the large corpus studied, we see that during the end of the reigns of the Kangxi and throughout that of Qianlong Emperors, European recipes were widely used (Fig. 4). In contrast, under the Yongzheng reign (1722-35), we note a certain return to Chinese technical solutions. These variations also appear regionally. Regarding the blue enamels studied in detail, there are observed differences between the Imperial workshops and those of Canton for export: the mixture of European and Chinese cobalt appears to be more common in the latter.[17] Technical analysis thus reveals a fascinating story of Chinese craftspeople adopting European techniques to produce objects for a European market with materials that had themselves already traveled along these same trade routes.
Philippe Colomban is CNRS Research Professor Emeritus at Sorbonne Université, MONARIS Laboratory, Paris
Acknowledgments: The author acknowledges co-workers and the staff and directors of the Musée du Louvre, Château de Fontainebleau, Cité de la Céramique, Musée national des arts asiatiques-Guimet, Musée des arts décoratifs, Musée de l’Ariana, Fondation baur, Musée des arts d’Extrême-Orient, as well as private collectors for the permission to analyze artefacts. This research was partially funded by the French Agence Nationale de la Recherche ANR EnamelFC project—19-CE27–0019-02.
[1] Philippe Colomban, Anh-Tu Ngo, and Nicolas Founery, “Non-Invasive Raman Analysis of 18th Century Chinese Export/Armorial Overglazed Porcelain: Identification of the Different Enamelling Techniques,” Heritage 5(2022): 233–59.
[2] Michèle Pirazzoli-t’Serstevens, “La céramique chinoise en Italie, XIIIe-début XVIe siècle,” Taoci 1 (205): 75-86; Pierre Verlet, “Le commerce des objets d’art et les marchands merciers à Paris au XVIIIe siècle,” Annales 13, no. 1 (1958): 10-29; Stéphane Castellucio, Le prince et le marchand. Le commerce de luxe chez les marchands merciers parisiens pendant le règne de Louis XIV (Paris: Editions S.P.M., 2014); John Finlay, Henri Bertin and the Representation of China in Eighteenth-Century France (New York: Routledge Research in Art History, 2020).
[3] Isabelle Landry-Deron, “La contribution des missionnaires aux arts du feu à la cour de Pékin (XVIIe-XVIIIe siècles),” Artefact 18 (2023): 117-37.
[4] Ching-Fei Shih, “L’Avènement d’une nouvelle palette de couleurs à Jingdezhen,” in Le secret des couleurs. Céramiques de Chine et d’Europe du XVIIIe siècle à nos jours, ed. Paulined’Abrigeon (Milan: 5 Continents Editions & Fondation baur, 2022), 21–59; Meg Chu-Ping Wang, “Eighteenth-Century Chinese Painted Enamelware Materials and Techniques,” Le secret des couleurs, 24-53; and Julie Bellemare, “A New Palette,” Journal of Glass Studies 64 (2022): 147-67.
[5] Philippe Colomban, Burcu Kırmızı, Catherine Gougeon, Michele Gironda and Catherine Cardinal, “Pigments and Glassy Matrix of the 17th-18th Century Enamelled French Watches: A Non-Invasive On-Site Raman and pXRF Study,” Journal of Cultural Heritage 44 (2020): 1-14.
[6] Philippe Colomban, Gulsu Simsek Franci, and Burcu Kırmızı, “Cobalt and Associated Impurities in Blue (and Green) Glass, Glaze and Enamel: Relationships between Raw Materials, Processing, Composition, Phases and International Trade,” Minerals 11 (2021): 633; Colomban et al., “Pigments and Glassy Matrix,” 1-14.
[7] Fukang Zhang, “The Origin and Development of Traditional Chinese Glazes and Decorative Ceramic Colours,” in Technology to Modern Science, Ceramics and Civilization Series, vol. 1, ed. Walter D. Kingery (Colombus, Ohio: The American Ceramic Society, 1985): 163–80; Walter D. Kingery and Pamela B. Vandiver, “The Eighteenth-Century Change in Technology and Style from the Famille-Verte Palette to the Famille-Rose Palette,” in Technology and Style, Ceramics and Civilization Series, vol. 2, ed. Walter D. Kingery (Colombus, Ohio: The American Ceramic Society, 1986), 363–81; Nigel Wood, Chinese Glazes (London: A & C Black Publishers Ltd, 1999).
[8] Landry-Deron, “La contribution des missionnaires,” 117-37.
[9] Zhang, “The Origin and Development of Traditional Chinese Glazes,” 163–80; Kingery and Vandiver, “The Eighteenth-Century Change in Technology and Style,” 363–81.
[10] Zhang, “The Origin and Development of Traditional Chinese Glazes,” 163–80; Wood, Chinese Glazes.
[11] Colomban, Franci, and Kırmızı, “Cobalt and Associated Impurities in Blue,” 633.
[12] Colomban, Franci, and Kırmızı, “Cobalt and Associated Impurities in Blue,” 633.
[13] Philippe Colomban, Yizheng Zhang, and Bing Zhao, “Non-Invasive Raman Analyses of Huafalang and Related Porcelain Wares. Searching for Evidence for Innovative Pigment Technologies,” Ceramic International 43, no.15 (2017): 12079-88; Philippe Colomban, Gulsu Simsek Franci, Jacques burlot, Xavier Gallet, bing, Zhao and Jean-baptiste Clais, “Non-Invasive On-Site pXRF Analysis of Colouring Agents, Marks and Enamels of Qing Imperial and Non-Imperial Porcelain,” Ceramics 6 (2023): 447-74.
[14] Colomban, Franci, and Kırmızı, “Cobalt and Associated Impurities in Blue,” 633.
[15] Colomban, Zhang, and Zhao, “Non-Invasive Raman Analyses of Huafalang,” 12079-88; Colomban et al., “Non-Invasive On-Site pXRF Analysis of Colouring Agents,” 447-74; Colomban, Franci, and Kırmızı, “Cobalt and Associated Impurities in Blue,” 633.
[16] Colomban, Zhang, and Zhao, “Non-Invasive Raman Analyses of Huafalang,” 12079-88; Colomban et al., “Non-Invasive On-Site pXRF Analysis of Colouring Agents,” 447-74.
[17] Philippe Colomban, Anh-Tu Ngo, and Nicolas Founery, 233–59; Colomban et al., “pXRF Data Evaluation Methodology for On-Site Analysis of Precious Artifacts,” 1752-78.
Cite this article as: Philippe Colomban, “The Quest for the Western Colors in China Under the Qing Emperors,” Journal18, Issue 17 Color (Spring 2024), https://www.journal18.org/7219.
Licence: CC BY-NC
Journal18 is published under a Creative Commons CC BY-NC International 4.0 license. Use of any content published in Journal18 must be for non-commercial purposes and appropriate credit must be given to the author of the content. Details for appropriate citation appear above.